工业4.0时代下MES系统
日期:2019-09-03 / 人气: / 来源:未知
工业4.0大趋势正影响着制造业的未来,全球市场瞬息万变,制造业必须有快速的应变能力,以满足客户的需求,创造新的市场机会。在我们所处的时代,信息科技、营运技术和全球大趋势来势汹汹,将改变制造业的商业模式。德国提出工业4.0时指出,其两大核心是智慧工厂与智能制造。工业4.0的目标是生产制造系统的数字化和虚拟化、将虚拟工厂与实际的对象结合起来、全面的点对点的信息通信、自配置和自矫正的适应能力以及使机器能集成人的作用,实现智能制造。
工业4.0的三大支柱是 MES系统 、虚拟与现实的结合和CPS,这也是智慧工厂的支撑技术。站在外部的视角,MES系统实现智慧工厂的服务化包装,对外提供标准服务接口,按照制造过程的“T、Q、C、S、E”组织生产。可以说,MES系统是智能制造在智慧工厂范畴内的承载主体,实现“物理工厂”的“信息领域”的投影。
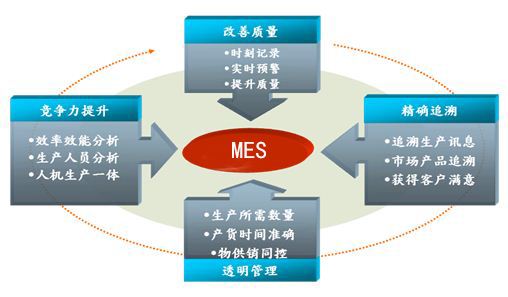
在智能制造的背景下,MES系统将实现传统的数字管理向智能管理模式转变,MES系统A组织给出MES系统功能模型的定义,强调生产过程“生产、质量、消耗及绩效”的业务管理。近十年来MES系统的发展,也是参考这个功能模型的定义,集中在业务数据采集、业务数据传递和业务统计。通过业务过程的数字化,建立了协同工作平台,并在此基础上进行数据分析与统计,基本实现了全面的数字化和透明化管理。但在实施MES系统的过程中都能深切感受到客户对MES系统智能化期望较高:希望能够采用APS自动实现作业任务编排,希望系统能够根据过程变化自动调整计划,希望自动调整工艺参数来确保质量最佳。但事实上,传统基于单据作业模式的MES系统,在数据分析与处理上并没有下太多的功夫。
在工业4.0时代,生产变化及灵活性更高,生产要素须自动配置,必然要求在生产全过程的数字化的基础上,增加智能优化方法。工厂的智能化分为两个层次,一个层次是实现微观层面的智能优化。比如在工序层面的控制中,在区域协调优化中采用智能化技术。或者在某一个专业领域,如设备的状态预测、质量预警及生产预警。另一个层面是宏观层面,根据生产过程中各要素的数字化,形成计划、排产、质量控制、过程跟踪的闭环反馈,采用智能优化算法进行协同优化。
从未来的需求来看,MES系统会从传统的集成向过程融合发展,尤其是在B2P的商业模式下,制造企业必须能够快速处理大量的单件制造及特别制造的方式,同时全球化驱动的分散性协同制造成为主流,这就导致了传统设计、计划到生产模式的反应迟缓,严谨的 PLM、ERP、MES系统的集成流程太过到刚性。取而代之的是一种新的方式是设计、计划和生产紧密协作、并行执行,基于同样的需求、物料、产能等数据,PLM设计结束之前,柔性生产计划即可快速下达,MES系统实时开始生产执行,同时实现良好的反馈机制。这种柔性协同也对系统间设计 BOM、生产BOM、数据、模型等一致性和灵活性提出了更高的要求。
工业4.0时代的MES系统,或许将重新定义,传统的车间管理将向工厂运营平台发展,在协同制造方面超越目前内部组织范畴,而扩展至与供应商和客户的连接;在制造智能方面将不限于收集、分析与展现,而将进一步实现现场实时分析、协同智能决策,及时调整制造执行过程;在业务领域层面,将扩展智能装备的性能监测与维护、绿色制造的能源管理等内容。在制造执行(Manufacturing Execution) 系统将跃变为卓越制造(Manufacturing Excellence)系统。
中国制造虽然有环境因素、资源因素,但最重要的因素来看,差在哪呢?分析认为,主要差在“软实力”方面。虽然在硬件层面我们也有明显的差距,但有大量数据比较得出,即使一样建设的生产线(如汽车生产线,我国的效率仍然和邻国日本差一大截,因此不能把责任推到基础硬件层面。工业4.0时代,传统的结构化数据向工业大数据平台发展,技术的发展为数据的产生(物联网)、存贮、分析(云技术)、使用(移动互联)更加方便。因此也可以说,工业4.0的变革是数据驱动型的变革。这个“软实力”提升的主要驱动力是“数据”的利用。MES系统传统上处理各类业务单据,数据仅限于结构化的数据,很多企业在此基础上,也开展了商务智能(BI)的建设与利用,但总体上还在有限的数据范围内进行事后分析。今天的物联网(包括设备、物料等IIOT及人工作业过程中的HIOT)将产生大量的实时信息,都是表征了生产过程的全息影像。这些数据在采集、管理、分析与可视化方面,技术上正在逐步可行。
在技术实现上,传统的MES系统在逐步开发及实施的过程中,功能一点点增加,传统的功能套件向模型驱动整合,最终形成覆盖工厂管理需要的一个功能套件集合,即我们常见的套装软件。但这种套装软件从设计本质上是以职能管理为核心的,以软件系统为中心的。在工业4.0时代,面向以客户为中心价值传递,以产品为中心的制造资源重组的要求时,传统的MES系统是无能为力的。有调查表明,在MES系统建成的三年内,50%的工艺(模型)将会或多或少随着生产的持续改进而调整,在工业4.0时代的定制时代这种变化更加剧烈。这就要求MES系统必须是一个可适应、可扩展的系统,其技术的主要特点是采用模型驱动技术来构架系统。将ISA95相关的、在制造业通用功能以组件的方式,而各厂不同的、适应各自管理及工艺流程的、不同应用系统集成的部分,将通过可配置的模型平台来实现。当工艺流程发生变化时,只需在线修改模型,而不需调整功能组件,从而实现系统的适应性。
从人机协同的角度来看,计算机技术发展到今天,主要存在两个问题没有很好解决。一是计算机的现场应用,一是信息的展示方法。试想,通过键盘、鼠标的信息录入方法完全是要求人们去适应计算机的需要,采用视窗操作界面,也是今天的计算机操作系统的展示信息的手段。这些都是以计算机为核心,或者说以系统为核心的思想。在工业4.0时代,MES系统也将从传统的视窗界面向虚拟现实转变,物联网技术引发数据海量增加、设备智能化及自主化管理,这些变化将人从“操作员”的角色逐步提升到“监控者及决策者”,人机交互的方式必须更加自然、实时、聚焦要点。虚拟现实及增强现实技术可以有效解决这一点。在工业4.0时代,虚拟世界将与现实世界高度融合。通过计算、自主控制和联网,人、机器和信息互相联接,融为一体,所有的生产数据将被全部整合到工厂虚拟现实管理系统中。利用三维可视化技术将生产场景真实展现出来,生产数据实时驱动三维场景中的设备,使其状态与真实生产场景一致,从而让管理者充分了解整个生产场景中各设备的运行状况,达到监测、查看、分析的目的。
目前,工业4.0相对来说仍处在起步阶段,工业4.0的关键是智能工厂,智能工厂是一种高能效的工厂,它基于高科技的、适应性强的的生产线。MES系统作为车间执行层面的制造执行系统,可帮助不同企业的不同需求,实现个性化智能工厂的构建,精益生产线,实现自动化生产。
工业4.0的三大支柱是 MES系统 、虚拟与现实的结合和CPS,这也是智慧工厂的支撑技术。站在外部的视角,MES系统实现智慧工厂的服务化包装,对外提供标准服务接口,按照制造过程的“T、Q、C、S、E”组织生产。可以说,MES系统是智能制造在智慧工厂范畴内的承载主体,实现“物理工厂”的“信息领域”的投影。
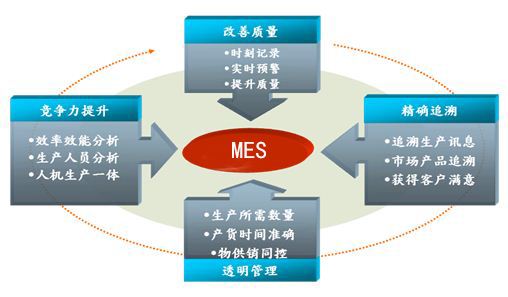
在智能制造的背景下,MES系统将实现传统的数字管理向智能管理模式转变,MES系统A组织给出MES系统功能模型的定义,强调生产过程“生产、质量、消耗及绩效”的业务管理。近十年来MES系统的发展,也是参考这个功能模型的定义,集中在业务数据采集、业务数据传递和业务统计。通过业务过程的数字化,建立了协同工作平台,并在此基础上进行数据分析与统计,基本实现了全面的数字化和透明化管理。但在实施MES系统的过程中都能深切感受到客户对MES系统智能化期望较高:希望能够采用APS自动实现作业任务编排,希望系统能够根据过程变化自动调整计划,希望自动调整工艺参数来确保质量最佳。但事实上,传统基于单据作业模式的MES系统,在数据分析与处理上并没有下太多的功夫。
在工业4.0时代,生产变化及灵活性更高,生产要素须自动配置,必然要求在生产全过程的数字化的基础上,增加智能优化方法。工厂的智能化分为两个层次,一个层次是实现微观层面的智能优化。比如在工序层面的控制中,在区域协调优化中采用智能化技术。或者在某一个专业领域,如设备的状态预测、质量预警及生产预警。另一个层面是宏观层面,根据生产过程中各要素的数字化,形成计划、排产、质量控制、过程跟踪的闭环反馈,采用智能优化算法进行协同优化。
从未来的需求来看,MES系统会从传统的集成向过程融合发展,尤其是在B2P的商业模式下,制造企业必须能够快速处理大量的单件制造及特别制造的方式,同时全球化驱动的分散性协同制造成为主流,这就导致了传统设计、计划到生产模式的反应迟缓,严谨的 PLM、ERP、MES系统的集成流程太过到刚性。取而代之的是一种新的方式是设计、计划和生产紧密协作、并行执行,基于同样的需求、物料、产能等数据,PLM设计结束之前,柔性生产计划即可快速下达,MES系统实时开始生产执行,同时实现良好的反馈机制。这种柔性协同也对系统间设计 BOM、生产BOM、数据、模型等一致性和灵活性提出了更高的要求。
工业4.0时代的MES系统,或许将重新定义,传统的车间管理将向工厂运营平台发展,在协同制造方面超越目前内部组织范畴,而扩展至与供应商和客户的连接;在制造智能方面将不限于收集、分析与展现,而将进一步实现现场实时分析、协同智能决策,及时调整制造执行过程;在业务领域层面,将扩展智能装备的性能监测与维护、绿色制造的能源管理等内容。在制造执行(Manufacturing Execution) 系统将跃变为卓越制造(Manufacturing Excellence)系统。
中国制造虽然有环境因素、资源因素,但最重要的因素来看,差在哪呢?分析认为,主要差在“软实力”方面。虽然在硬件层面我们也有明显的差距,但有大量数据比较得出,即使一样建设的生产线(如汽车生产线,我国的效率仍然和邻国日本差一大截,因此不能把责任推到基础硬件层面。工业4.0时代,传统的结构化数据向工业大数据平台发展,技术的发展为数据的产生(物联网)、存贮、分析(云技术)、使用(移动互联)更加方便。因此也可以说,工业4.0的变革是数据驱动型的变革。这个“软实力”提升的主要驱动力是“数据”的利用。MES系统传统上处理各类业务单据,数据仅限于结构化的数据,很多企业在此基础上,也开展了商务智能(BI)的建设与利用,但总体上还在有限的数据范围内进行事后分析。今天的物联网(包括设备、物料等IIOT及人工作业过程中的HIOT)将产生大量的实时信息,都是表征了生产过程的全息影像。这些数据在采集、管理、分析与可视化方面,技术上正在逐步可行。
在技术实现上,传统的MES系统在逐步开发及实施的过程中,功能一点点增加,传统的功能套件向模型驱动整合,最终形成覆盖工厂管理需要的一个功能套件集合,即我们常见的套装软件。但这种套装软件从设计本质上是以职能管理为核心的,以软件系统为中心的。在工业4.0时代,面向以客户为中心价值传递,以产品为中心的制造资源重组的要求时,传统的MES系统是无能为力的。有调查表明,在MES系统建成的三年内,50%的工艺(模型)将会或多或少随着生产的持续改进而调整,在工业4.0时代的定制时代这种变化更加剧烈。这就要求MES系统必须是一个可适应、可扩展的系统,其技术的主要特点是采用模型驱动技术来构架系统。将ISA95相关的、在制造业通用功能以组件的方式,而各厂不同的、适应各自管理及工艺流程的、不同应用系统集成的部分,将通过可配置的模型平台来实现。当工艺流程发生变化时,只需在线修改模型,而不需调整功能组件,从而实现系统的适应性。
从人机协同的角度来看,计算机技术发展到今天,主要存在两个问题没有很好解决。一是计算机的现场应用,一是信息的展示方法。试想,通过键盘、鼠标的信息录入方法完全是要求人们去适应计算机的需要,采用视窗操作界面,也是今天的计算机操作系统的展示信息的手段。这些都是以计算机为核心,或者说以系统为核心的思想。在工业4.0时代,MES系统也将从传统的视窗界面向虚拟现实转变,物联网技术引发数据海量增加、设备智能化及自主化管理,这些变化将人从“操作员”的角色逐步提升到“监控者及决策者”,人机交互的方式必须更加自然、实时、聚焦要点。虚拟现实及增强现实技术可以有效解决这一点。在工业4.0时代,虚拟世界将与现实世界高度融合。通过计算、自主控制和联网,人、机器和信息互相联接,融为一体,所有的生产数据将被全部整合到工厂虚拟现实管理系统中。利用三维可视化技术将生产场景真实展现出来,生产数据实时驱动三维场景中的设备,使其状态与真实生产场景一致,从而让管理者充分了解整个生产场景中各设备的运行状况,达到监测、查看、分析的目的。
目前,工业4.0相对来说仍处在起步阶段,工业4.0的关键是智能工厂,智能工厂是一种高能效的工厂,它基于高科技的、适应性强的的生产线。MES系统作为车间执行层面的制造执行系统,可帮助不同企业的不同需求,实现个性化智能工厂的构建,精益生产线,实现自动化生产。
作者:hzjuxadmin
上一篇:MES系统为企业带来的六大价值
下一篇:MES系统设备生产数据可视化
推荐内容 Recommended
相关内容 Related
- MES制造执行系统生产计划管理01-10
- MES系统,生产制造很给力01-09
- MES系统中生产运行系统的重要性01-08
- MES系统三大层结构01-07
- MES系统的五大功能、六大好处01-06