MES系统设备生产数据可视化
日期:2019-09-04 / 人气: / 来源:未知
MES系统 信息化与工业化快速融合,信息技术渗透到了离散制造企业产业链的各个环节技术在离散制造企业中得到广泛应用,尤其是新一代信息技术在工业领域的应用,离散制造企业也进入了互联网工业的新的发展阶段,所拥有的数据也日益丰富。MES系统离散制造企业生产线处于高速运转,由生产设备所产生采集和处理的数据量远大于企业中计算机和人工产生的数据,对数据的实时性要求也更高。
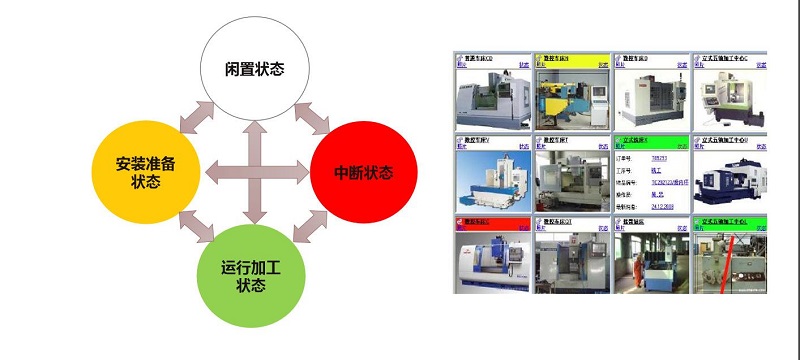
MES系统中获得主生产计划及生产准备相关信息后,进行车间计划排产,并将生产任务下发给系统安排数控加工,将检验任务下发给质量系统用于质量跟踪。同时,MES通过数据采集系统获得生产过程中的任务执行和人员等信息,用于生产过程监控和车间事件处理。在MES系统产品功能的基础上,与时俱进,不断进行创新和优化,向着更强的集成化、更强的实时性和更强的模块化发展,打造汽车行业MES系统品牌,同时向汽车零部件和离散制造业发展。自主开发实施周期长系统维护复杂但应用见效快;选择成熟产品,实施周期短系统维护工作量小,但应用见效慢。MES系统选择自主开发的企业大多具有一定的实施背景条件合作中引入了某原型软件并进行消化吸收。对于国内大多数企业来说,选择成熟产品进行适当二次开发是一种更为明智的做法。
流程型企业和离散制造企业不一样对MES就很重视,以至于产生了像在MES中打出一片天的企业。本身管理的复杂性、质量要求和颗粒度决定了MES天然的重要性。制造业的支柱产业,由于产品本身的复杂性,及的订单生产方式,决定了其生产不同于一般产品,
从我的理解,未来用户定制化的需求会越来越成为一个重要分支。这并不会完全取代大规模自动化生产,而是形成有机的结合。MES系统制造业价值创造和分配模式正在发生转变,借助互联网平台,企业、客户及利益相关方纷纷参与到价值创造、价值传递及价值实现等生产制造的各个环节。个性化定制把前端的研发设计交给了用户;用户直接向企业下达订单,也弱化了后端的销售,从而拉平并重新结合成价值环。
MES系统离散制造业自身的特性导致生产计划调度困难,离散制造业企业生产过程是断续的,生产工艺过程随零件不同而不同,零件品种规格多,产品结构复杂,使得生产计划调度十分困难。MES系统控制优化是实现敏捷化生产管理与运行的核心,对于离散式制造业,车间一直处于动态变化和不确定的制造环境。实际的车间业务过程较为复杂,与生产环境相关各种因素经常变化,各种不确定性事件经常发生等,使得计划排产更频繁生产调度更复杂。
MES系统可对不同车型进行工艺路径的设置,在排产或上线时,根据车辆属性自动匹配工艺路径。生产制造过程的工序检验与产品质量管理,能够实现对工序检验与产品质量过程追溯,对不合格品以及整改过程进行严格控制。MES系统实现生产过程关键要素的全面记录以及完备的质量追溯,准确统计产品的合格率和不合格率,为质量改进提供量化指标。根据产品质量分析结果,对出厂产品进行预防性维护。MES系统运用物联网技术工业企业可以将机器等生产设施接入互联网,构建网络化物理设备系统,进而使各生产设备能够自动交换信息、触发动作和实施控制。物联网技术有助于加快生产制造实时数据信息的感知,加快生产资源的优化配置,实现过程虚拟化。
MES系统的实施难度要源于MES产品和行业差异大,由于MES涉及的业务和人员范围较广,对于企业来说,如今客户的需求正越来越个性化,因此企业必须快速找出解决方案,应对客户的新需求。而很多破坏性、具有颠覆性的商业模式也在改变现有的企业组织结构——对于制造商而言,实现更高的出产率而且制造小组件的能力要更精细。MES生产制造执行系统作为企业生产计划层和生产制程执行系统的桥梁,通过信息传递对从订单下达到产品完成的整个生产过程进行优化管理。MES还通过双向的直接通讯在企业内部和整个产品供应链中提供有关产品行为的关键任务信息。
MES系统通过直观的图形、数字表示,系统提供机床负荷以及每台机床生产任务的视图及分析功能,可方便地优化生产和平衡机床负荷,使生产计划更科学更合理。对逾期计划,系统可提供工序拆分、外协加工、调整设备、调整优先级等灵活的处理措施。通用性和可配置性较差,现有MES系统针对的只是某些特定的需求,难以应对企业业务流程的重组和变更。针对基于数据集成技术的工厂数据模型的不足,使系统的可配置性,可重构性,可扩展性差, 限制了推广和应用MES系统范围。智能制造也需要加强平台建设,让行业、企业、科研院所等各方广泛参与,共同谋划如何具体落实中国制造智能升级的路线图,支持多种高级自动排产算法,多种排产方式,可满足企业各类复杂的排产要求。
对改善效果标准化,制定再发防止措施,落实到相关管理文件。面向订单生产,由于订单规格、数量、交货期变化大,每种产品都有其特殊性,从产品订货决策到制造全过程,每一种产品都具有一定的独立性,企业必须按订单组织生产。是企业管理中使用成熟的系统,MES虽然可以与之兼容,但从本质上来说,是企业运营管理的系统,MES是生产制造的系统,两套系统数据集成如何匹配是企业头疼的一大问题。
MES系统数据采集和数据分析系统利用系统提供的机床联网自动采集功能和触摸屏、扫描枪等手工采集方式进行车间数据采集,这些数据传递给MES系统用于生产监控,与质量相关的信息则传递给用于质量跟踪、问题处理及统计分析。企业的管理难点、痛点和实际需求唯有自身清楚,不同行业或处于同一行业的不同企业都有可能大相径庭,况且不同公司的企业文化和管理理念都存在明显的差异,无实施目标、无指导思想、无匹配框架的MES方案是空虚的、乏力的,也不会有可借鉴的实质性内容。企业在要求MES系统开发商出具技术方案时,应有所导向和聚焦,使其在限定的框架范围内精工细作,不能任其发挥。MES系统开发商可能接触的案例或业绩较多,但在企业具体运作和实际需求上不甚了解,难免会在企业诊断层面,从而影响MES系统的落地执行,因此在MES开发商引导过程中一定要严格把控是否与自身企业相适应。
对执行过程进行跟踪检查,出现偏差及时修正;基于这个出发点,工业4.0首先要解决的是,基于互联网技术,线上和线下融合,能充分对应各种订单,尤其是个性化订单,由工业3.0时代的销售自动化发展而来的销售智能化系统。由于MES系统是一项较为复杂的大型管理系统,模块众多、涉及的技术也非常多,MES系统通过现场的数据收集,建立起物料、设备、人员、工具、半成品、成品之间的关联关系,保证信息的继承性与可追溯性。系统提供的实时数据,既可以向生产 管理人员提供车间作业和设备的实际状况,也可以向业务部门提供客户订单的生产情况,还能够根据实际生产的情况计算出直接物料耗用成本。基于现场数据的报表 和查询功能,能为高层管理人员的决策提供支持。减少了大量的统计工作,并增加了统计的全面性与可靠性,实现制造数据的可追溯性。
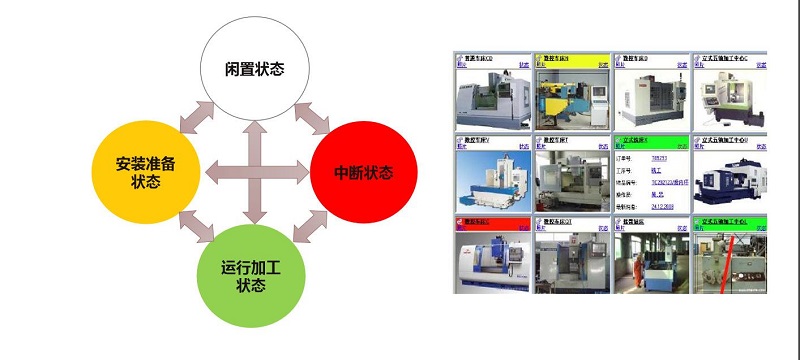
MES系统中获得主生产计划及生产准备相关信息后,进行车间计划排产,并将生产任务下发给系统安排数控加工,将检验任务下发给质量系统用于质量跟踪。同时,MES通过数据采集系统获得生产过程中的任务执行和人员等信息,用于生产过程监控和车间事件处理。在MES系统产品功能的基础上,与时俱进,不断进行创新和优化,向着更强的集成化、更强的实时性和更强的模块化发展,打造汽车行业MES系统品牌,同时向汽车零部件和离散制造业发展。自主开发实施周期长系统维护复杂但应用见效快;选择成熟产品,实施周期短系统维护工作量小,但应用见效慢。MES系统选择自主开发的企业大多具有一定的实施背景条件合作中引入了某原型软件并进行消化吸收。对于国内大多数企业来说,选择成熟产品进行适当二次开发是一种更为明智的做法。
流程型企业和离散制造企业不一样对MES就很重视,以至于产生了像在MES中打出一片天的企业。本身管理的复杂性、质量要求和颗粒度决定了MES天然的重要性。制造业的支柱产业,由于产品本身的复杂性,及的订单生产方式,决定了其生产不同于一般产品,
从我的理解,未来用户定制化的需求会越来越成为一个重要分支。这并不会完全取代大规模自动化生产,而是形成有机的结合。MES系统制造业价值创造和分配模式正在发生转变,借助互联网平台,企业、客户及利益相关方纷纷参与到价值创造、价值传递及价值实现等生产制造的各个环节。个性化定制把前端的研发设计交给了用户;用户直接向企业下达订单,也弱化了后端的销售,从而拉平并重新结合成价值环。
MES系统离散制造业自身的特性导致生产计划调度困难,离散制造业企业生产过程是断续的,生产工艺过程随零件不同而不同,零件品种规格多,产品结构复杂,使得生产计划调度十分困难。MES系统控制优化是实现敏捷化生产管理与运行的核心,对于离散式制造业,车间一直处于动态变化和不确定的制造环境。实际的车间业务过程较为复杂,与生产环境相关各种因素经常变化,各种不确定性事件经常发生等,使得计划排产更频繁生产调度更复杂。
MES系统可对不同车型进行工艺路径的设置,在排产或上线时,根据车辆属性自动匹配工艺路径。生产制造过程的工序检验与产品质量管理,能够实现对工序检验与产品质量过程追溯,对不合格品以及整改过程进行严格控制。MES系统实现生产过程关键要素的全面记录以及完备的质量追溯,准确统计产品的合格率和不合格率,为质量改进提供量化指标。根据产品质量分析结果,对出厂产品进行预防性维护。MES系统运用物联网技术工业企业可以将机器等生产设施接入互联网,构建网络化物理设备系统,进而使各生产设备能够自动交换信息、触发动作和实施控制。物联网技术有助于加快生产制造实时数据信息的感知,加快生产资源的优化配置,实现过程虚拟化。
MES系统的实施难度要源于MES产品和行业差异大,由于MES涉及的业务和人员范围较广,对于企业来说,如今客户的需求正越来越个性化,因此企业必须快速找出解决方案,应对客户的新需求。而很多破坏性、具有颠覆性的商业模式也在改变现有的企业组织结构——对于制造商而言,实现更高的出产率而且制造小组件的能力要更精细。MES生产制造执行系统作为企业生产计划层和生产制程执行系统的桥梁,通过信息传递对从订单下达到产品完成的整个生产过程进行优化管理。MES还通过双向的直接通讯在企业内部和整个产品供应链中提供有关产品行为的关键任务信息。
MES系统通过直观的图形、数字表示,系统提供机床负荷以及每台机床生产任务的视图及分析功能,可方便地优化生产和平衡机床负荷,使生产计划更科学更合理。对逾期计划,系统可提供工序拆分、外协加工、调整设备、调整优先级等灵活的处理措施。通用性和可配置性较差,现有MES系统针对的只是某些特定的需求,难以应对企业业务流程的重组和变更。针对基于数据集成技术的工厂数据模型的不足,使系统的可配置性,可重构性,可扩展性差, 限制了推广和应用MES系统范围。智能制造也需要加强平台建设,让行业、企业、科研院所等各方广泛参与,共同谋划如何具体落实中国制造智能升级的路线图,支持多种高级自动排产算法,多种排产方式,可满足企业各类复杂的排产要求。
对改善效果标准化,制定再发防止措施,落实到相关管理文件。面向订单生产,由于订单规格、数量、交货期变化大,每种产品都有其特殊性,从产品订货决策到制造全过程,每一种产品都具有一定的独立性,企业必须按订单组织生产。是企业管理中使用成熟的系统,MES虽然可以与之兼容,但从本质上来说,是企业运营管理的系统,MES是生产制造的系统,两套系统数据集成如何匹配是企业头疼的一大问题。
MES系统数据采集和数据分析系统利用系统提供的机床联网自动采集功能和触摸屏、扫描枪等手工采集方式进行车间数据采集,这些数据传递给MES系统用于生产监控,与质量相关的信息则传递给用于质量跟踪、问题处理及统计分析。企业的管理难点、痛点和实际需求唯有自身清楚,不同行业或处于同一行业的不同企业都有可能大相径庭,况且不同公司的企业文化和管理理念都存在明显的差异,无实施目标、无指导思想、无匹配框架的MES方案是空虚的、乏力的,也不会有可借鉴的实质性内容。企业在要求MES系统开发商出具技术方案时,应有所导向和聚焦,使其在限定的框架范围内精工细作,不能任其发挥。MES系统开发商可能接触的案例或业绩较多,但在企业具体运作和实际需求上不甚了解,难免会在企业诊断层面,从而影响MES系统的落地执行,因此在MES开发商引导过程中一定要严格把控是否与自身企业相适应。
对执行过程进行跟踪检查,出现偏差及时修正;基于这个出发点,工业4.0首先要解决的是,基于互联网技术,线上和线下融合,能充分对应各种订单,尤其是个性化订单,由工业3.0时代的销售自动化发展而来的销售智能化系统。由于MES系统是一项较为复杂的大型管理系统,模块众多、涉及的技术也非常多,MES系统通过现场的数据收集,建立起物料、设备、人员、工具、半成品、成品之间的关联关系,保证信息的继承性与可追溯性。系统提供的实时数据,既可以向生产 管理人员提供车间作业和设备的实际状况,也可以向业务部门提供客户订单的生产情况,还能够根据实际生产的情况计算出直接物料耗用成本。基于现场数据的报表 和查询功能,能为高层管理人员的决策提供支持。减少了大量的统计工作,并增加了统计的全面性与可靠性,实现制造数据的可追溯性。
作者:hzjuxadmin
上一篇:工业4.0时代下MES系统
下一篇:汽车零部件行业MES系统
推荐内容 Recommended
相关内容 Related
- MES制造执行系统生产计划管理01-10
- MES系统,生产制造很给力01-09
- MES系统中生产运行系统的重要性01-08
- MES系统三大层结构01-07
- MES系统的五大功能、六大好处01-06