汽车零部件MES系统软件解决方案(五)
日期:2018-06-10 / 人气: / 来源:未知
1.3.2.2.3、汽车零部件 MES系统 软件在制品动态流量监控系统
1.3.2.2.3.1、需求背景
正常情况下,生产系统按照计划的生产节拍进行生产,上下道工序的在制品流转非常顺畅。在一切条件都理想的情况下,系统里的生产计 划会完成的很好。但是,现实的生产系统中往往隐藏着许多不确定因素,导致达成计划的过程容易出现风险。例如,我们通常认为只要保 证瓶颈产能的产出,就能够提升整体的产销率。但有时非瓶颈工序由于某种原因(新手/设备异常/品质异常)变成了非瓶颈工序。那么我 们构建的计划模型就不那么乐观了。另外,对于瓶颈工序本身同样也需要注意由于异常导致的生产节拍降低。希望避免这些异常带来的影 响,生产系统就需要在异常还没有造成太大影响时及时得到纠正处理。实际上我们需要有一套系统能够实时监控生产线各个工序的在制品 流转节拍(我们称为在制品动态流量)。一旦发生异常时候能够及时反馈到管理层,让管理层及时响应异常。这套系统就是我们需要在汽 车零部件MES系统软件解决方案引入的在制品动态流量监控系统。
1.3.2.2.3.2、实现原理
首先,汽车零部件MES系统软件在生产线对设备进行联网监控,对手工作业的工序安装辅助设备(例如红外线感应器)自动采集工序的在 制品产出量。其次,系统提供生产单位(设备/班组)在生产不同产品时的单位时间产能配置。并设定监控时间间隔以及预警下限,汽车 零部件MES系统软件根据节拍时间对产线对应生产单位的实际产出量进行差异比对。当实际产量低于节拍内的计划产量,且超出预警下限 量则触发系统预警机制。
当触发预警,管理部门应快速排查原因,涉及的责任人员需在时效范围内处理异常。否则,预警机制采取异常逐级上报的机制向上级管理 单位汇报异常。
1.3.2.2.3.3、作用分析
汽车零部件MES系统软件通过应用在制品动态流量监控系统必然带来以下效果:
避免非瓶颈工序变成瓶颈;
确保瓶颈工序正常的生产节拍;
实时监控,异常还未造成太大影响时就纠正处理了,从而达到事前预警的目的;
避免由于异常导致的生产计划Delay;
降低由于生产计划Delay带来的各个业务部门协同成本。
1.3.2.2.4、汽车零部件MES系统软件设备OEE监控系统
1.3.2.2.4.1、需求背景
每一个生产设备都有自己的理论产能,要实现这一理论产能必须保证没有任何干扰和质量损耗。OEE就是用来表现实际的生产能力相对于 理论产能的比率,它是一个独立的测量工具。监控设备自动分析设备的OEE是当前生产型企业重要的信息化需求。
1.3.2.2.4.2、实现原理
OEE的组成包含三大指标:时间稼动率(可用率),性能稼动率(表现指数),良品率(质量指数),相关指标均可通过汽车零部件MES系 统软件产品得出。
时间稼动率(可用率),系统通过采集设备负荷运行时间以及停机时间得出设备可用率。
性能稼动率(表现指数),系统通过理论节拍时间、实际投入数量、以及实际稼动时间得出表现指数。
良品率(质量指数),系统通过投入数量、不良数量得出质量指数。

首先,汽车零部件MES系统软件对生产线的每台生产设备部署设备终端并进行统一联网。从而形成对设备的实时监控,采集计算设备OEE的 相关数据。其次,通过PDCA管理循环不断提高设备OEE。最后,OEE必须与精益原则相符,且不应该是片面的要求提高OEE,要确保对OEE的 采取的一系列措施不会导致在制品库存的冗余。汽车零部件MES系统软件引入的TOC理论即是遵循了这种规范。
设备OEE的PDCA管理循环
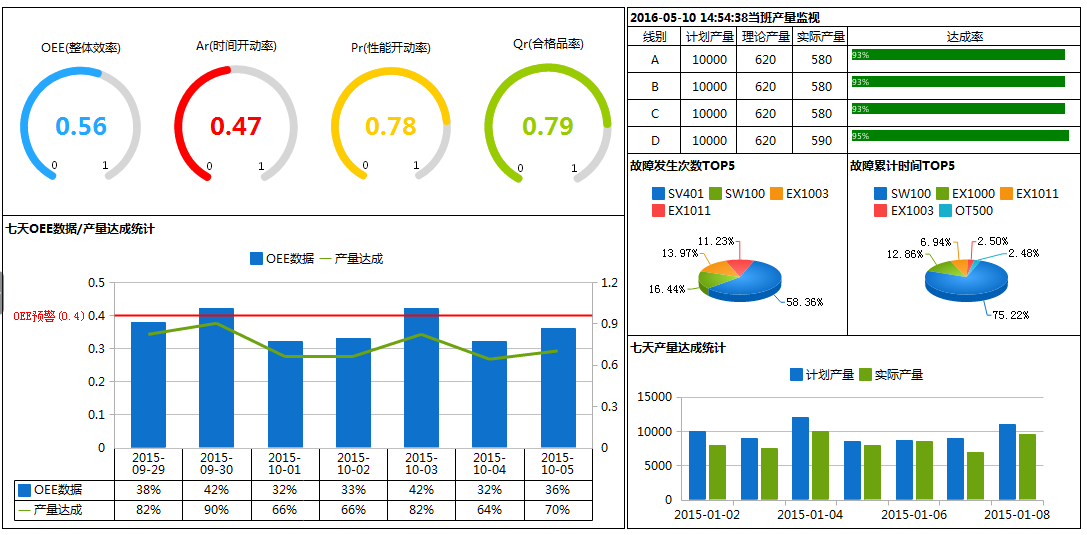
为每台设备制定 OEE计划标准,将标准集成到系统中;
系统对设备进行实时监控,汇总分析设备的实际执行OEE数据;
每天通过可视化看板显示存在OEE标准与实际执行出现差异的设备;
进一步可查看导致差异的原因;
当出现差异时,通过消息机制逐级汇总到相关管理人员;
通过多维度的KPI考核客观反馈设备以及相关管理人员的绩效;
采取改善措施,制定新的OEE标准,进行下一个PDCA管理循环。
1.3.2.2.4.3、作用分析
汽车零部件 MES系统软件 通过应用设备OEE监控系统必然带来以下效果:
方便领导宏观查阅生产状况和了解生产信息;
使机台设备保持良好的正常运转;
使人力与机台设备科学配合,发挥出最大化的潜能;
可以帮助管理者发现和减少生产中存在的六大损失;
可以征对问题,分析和改善生产状况及产品质量;
能最大化提高资源和设备的利用率,挖掘出最大的生产潜力;
1.3.2.2.3.1、需求背景
正常情况下,生产系统按照计划的生产节拍进行生产,上下道工序的在制品流转非常顺畅。在一切条件都理想的情况下,系统里的生产计 划会完成的很好。但是,现实的生产系统中往往隐藏着许多不确定因素,导致达成计划的过程容易出现风险。例如,我们通常认为只要保 证瓶颈产能的产出,就能够提升整体的产销率。但有时非瓶颈工序由于某种原因(新手/设备异常/品质异常)变成了非瓶颈工序。那么我 们构建的计划模型就不那么乐观了。另外,对于瓶颈工序本身同样也需要注意由于异常导致的生产节拍降低。希望避免这些异常带来的影 响,生产系统就需要在异常还没有造成太大影响时及时得到纠正处理。实际上我们需要有一套系统能够实时监控生产线各个工序的在制品 流转节拍(我们称为在制品动态流量)。一旦发生异常时候能够及时反馈到管理层,让管理层及时响应异常。这套系统就是我们需要在汽 车零部件MES系统软件解决方案引入的在制品动态流量监控系统。
1.3.2.2.3.2、实现原理
首先,汽车零部件MES系统软件在生产线对设备进行联网监控,对手工作业的工序安装辅助设备(例如红外线感应器)自动采集工序的在 制品产出量。其次,系统提供生产单位(设备/班组)在生产不同产品时的单位时间产能配置。并设定监控时间间隔以及预警下限,汽车 零部件MES系统软件根据节拍时间对产线对应生产单位的实际产出量进行差异比对。当实际产量低于节拍内的计划产量,且超出预警下限 量则触发系统预警机制。
当触发预警,管理部门应快速排查原因,涉及的责任人员需在时效范围内处理异常。否则,预警机制采取异常逐级上报的机制向上级管理 单位汇报异常。
1.3.2.2.3.3、作用分析
汽车零部件MES系统软件通过应用在制品动态流量监控系统必然带来以下效果:
避免非瓶颈工序变成瓶颈;
确保瓶颈工序正常的生产节拍;
实时监控,异常还未造成太大影响时就纠正处理了,从而达到事前预警的目的;
避免由于异常导致的生产计划Delay;
降低由于生产计划Delay带来的各个业务部门协同成本。
1.3.2.2.4、汽车零部件MES系统软件设备OEE监控系统
1.3.2.2.4.1、需求背景
每一个生产设备都有自己的理论产能,要实现这一理论产能必须保证没有任何干扰和质量损耗。OEE就是用来表现实际的生产能力相对于 理论产能的比率,它是一个独立的测量工具。监控设备自动分析设备的OEE是当前生产型企业重要的信息化需求。
1.3.2.2.4.2、实现原理
OEE的组成包含三大指标:时间稼动率(可用率),性能稼动率(表现指数),良品率(质量指数),相关指标均可通过汽车零部件MES系 统软件产品得出。
时间稼动率(可用率),系统通过采集设备负荷运行时间以及停机时间得出设备可用率。
性能稼动率(表现指数),系统通过理论节拍时间、实际投入数量、以及实际稼动时间得出表现指数。
良品率(质量指数),系统通过投入数量、不良数量得出质量指数。

首先,汽车零部件MES系统软件对生产线的每台生产设备部署设备终端并进行统一联网。从而形成对设备的实时监控,采集计算设备OEE的 相关数据。其次,通过PDCA管理循环不断提高设备OEE。最后,OEE必须与精益原则相符,且不应该是片面的要求提高OEE,要确保对OEE的 采取的一系列措施不会导致在制品库存的冗余。汽车零部件MES系统软件引入的TOC理论即是遵循了这种规范。
设备OEE的PDCA管理循环
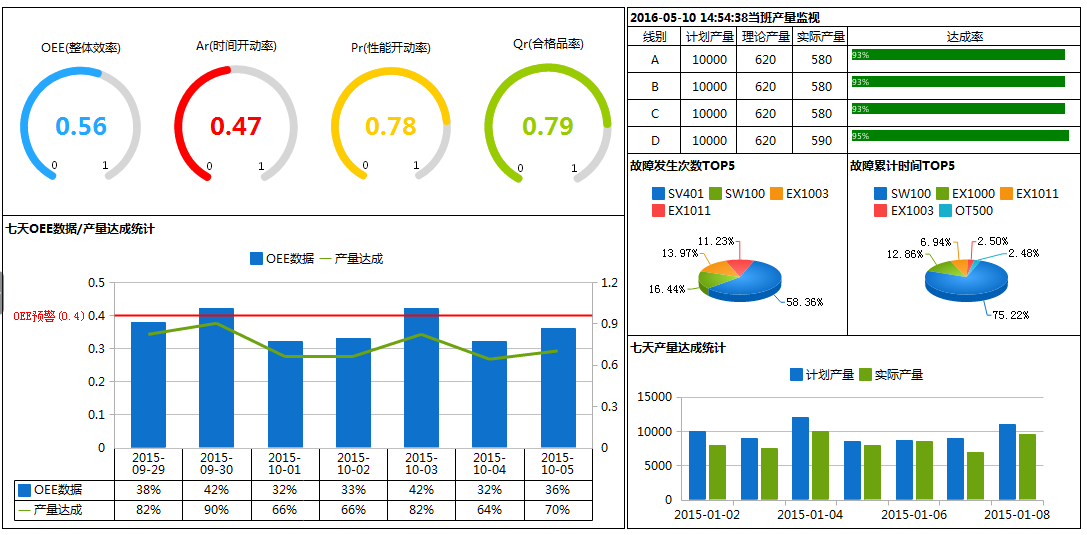
为每台设备制定 OEE计划标准,将标准集成到系统中;
系统对设备进行实时监控,汇总分析设备的实际执行OEE数据;
每天通过可视化看板显示存在OEE标准与实际执行出现差异的设备;
进一步可查看导致差异的原因;
当出现差异时,通过消息机制逐级汇总到相关管理人员;
通过多维度的KPI考核客观反馈设备以及相关管理人员的绩效;
采取改善措施,制定新的OEE标准,进行下一个PDCA管理循环。
1.3.2.2.4.3、作用分析
汽车零部件 MES系统软件 通过应用设备OEE监控系统必然带来以下效果:
方便领导宏观查阅生产状况和了解生产信息;
使机台设备保持良好的正常运转;
使人力与机台设备科学配合,发挥出最大化的潜能;
可以帮助管理者发现和减少生产中存在的六大损失;
可以征对问题,分析和改善生产状况及产品质量;
能最大化提高资源和设备的利用率,挖掘出最大的生产潜力;
作者:hzjuxadmin
推荐内容 Recommended
相关内容 Related
- MES系统,生产制造很给力01-09
- MES系统中生产运行系统的重要性01-08
- MES系统三大层结构01-07
- MES系统的五大功能、六大好处01-06
- MES系统与ERP系统的数据交互01-03