某汽车行业MES系统软件解决方案(五)
日期:2018-05-29 / 人气: / 来源:未知
3.1.2.3、物流走向及物流道具精益化不够
公司整体布局及工序分布相对合理,整个物流走向按照工艺流程进行布置,由于厂房设计及工艺限制,将各个工序进行分车间管理,主要分为注塑、制版、喷漆、总装、包装及仓储几个车间,主要工艺流程如下(制版及分装未纳入):

在整个工艺流分布过程中,喷漆车间为工艺分割最多的车间,其工艺复杂程度较高,并分成了几个独立的小模块,该车间管控难度较大,由于工艺问题上下工序衔接经常出问题,这也使得喷漆车间成为公司生产运营过程中的盲区,无法量化的工艺设定导致产品在该区域生产过程无法进行监控,该车间建立流水模式及数据采集显现的需求相对迫切。
从工艺走向来看,整个物流过程充满了搬运及WIP堆放的浪费,几乎每个工序都需要进行搬运和堆放,从精益角度看,每个工序都存在浪费;
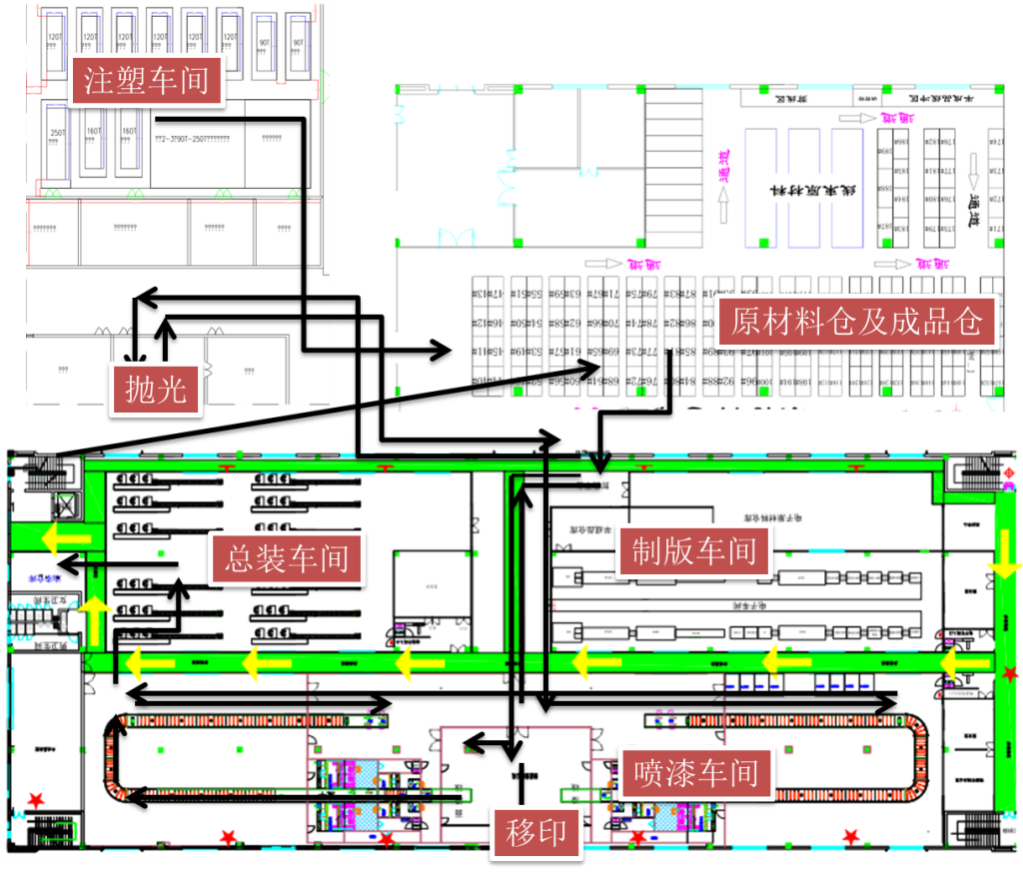
图3:公司产品实物流转图
在整个实物流转图中,由于布局的限制,使得注塑与其他车间的搬运距离相对较远,在喷漆车间内部出现的搬运情况较为严重,物料从原材料仓库到喷漆车间一直到从喷漆车间出去到总装,整个物流距离接近1800米(包含到抛光并返回),还不算工序内部兜转距离;车间内部搬运距离过长,使得喷漆整体无法把控。
内部物流主要依托流转小车及搬运车,但对搬运频次、搬运容量、搬运时间并未做相应标准,使得搬运过程随意性大。
3.1.2.4、内部计划协调性差,计划达成率不高
由于车间内部基础数据的缺失而无法进行工序工时估算、车间内部物流相对混乱而无法制定标准管理道具及辅助工具,使得公司在计划协调性上柔性不足,又由于销售预测及采购上的不确定因素过多,使得计划生产难度加大,销售被迫妥协生产,生产又由于订单及内部问题导致计划达成率低。
单从喷涂计划实施来看,整个计划模式在此车间运行几乎毫无规则,物流部针对喷涂下达的也仅仅只是周计划,无法落实具体的当日计划,更无法对喷涂进行产能管控,导致整个生产计划被喷涂计划全部打乱,依照模糊的计划进行生产的喷涂车间内部也没有进行相应的管控措施,包括物料供给方式也无法确定,使得喷涂车间变成整个生产部门的黑匣子,产品什么时候出来没有人能真正得知。
从计划实施上看,对于相对能够预估产能的车间部门,计划都制定了相应详细的周、日预估,而对于急需改进的喷涂车间却只有周计划,无法协同的生产模式注定每个区块的效率都无法达到最优值。

(图4、总体达成情况)
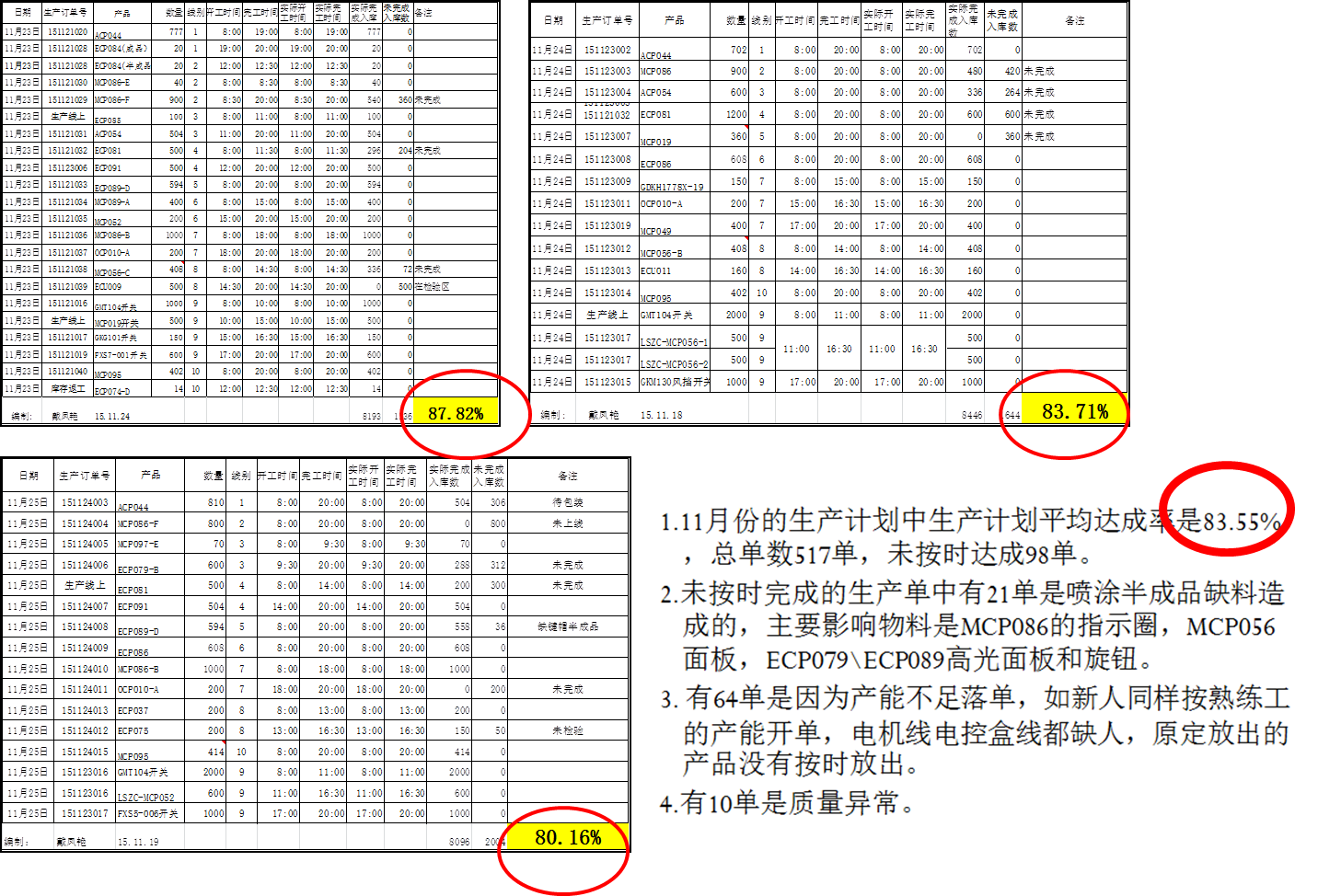
(图5、11月份计划达成率)
每个车间都有不同的生产计划,计划协同性及优先级无法整体体现,所以喷涂依据总装计划混合生产,销售插单将总装计划打乱,进而整个计划被打乱。
3.2 某汽车行业MES系统软件精益整体化解决措施
3.2.1 精益整体规划设计
某汽车行业MES系统软件精益整体理念构建框架:
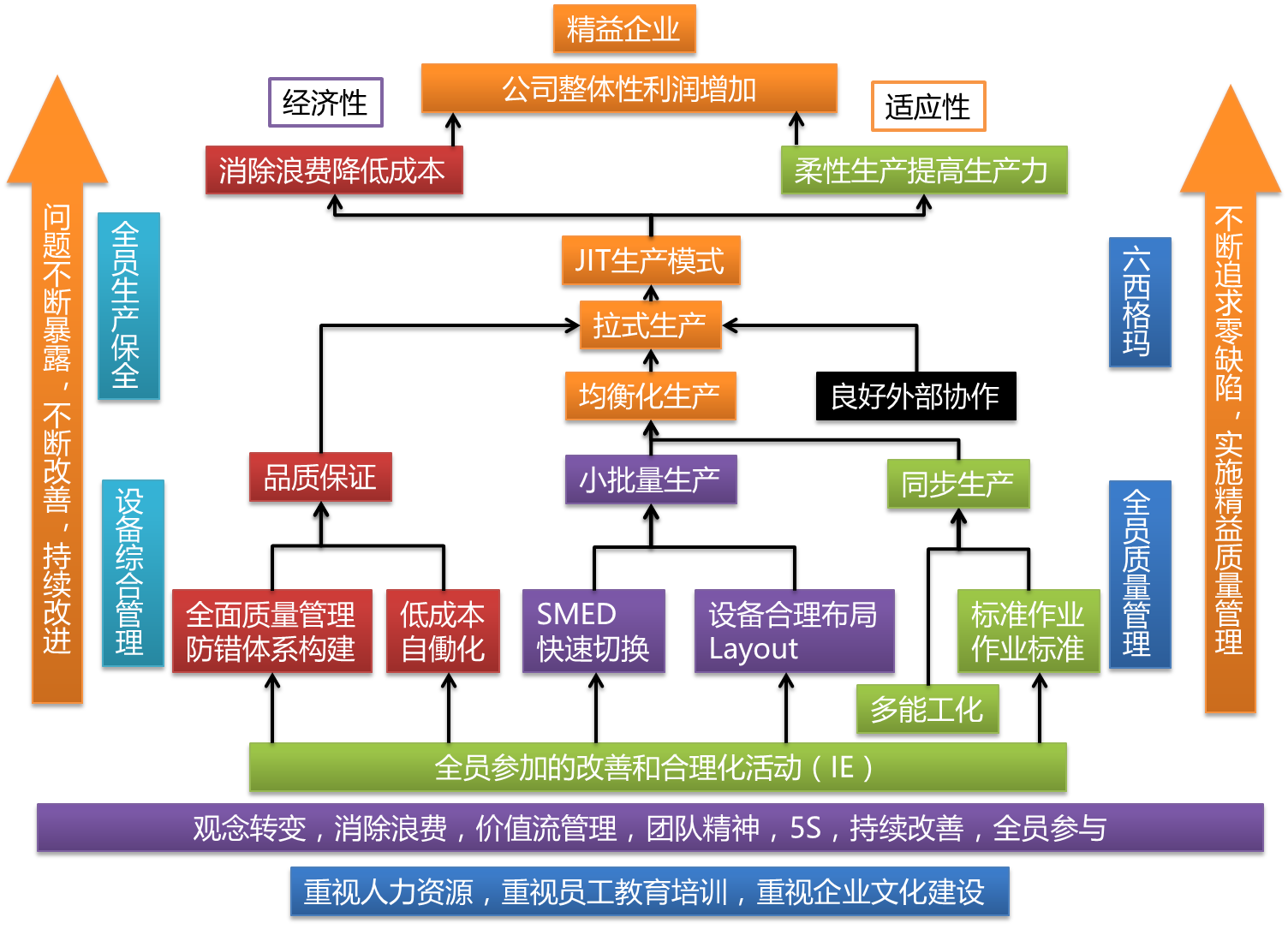
依据该公司管理特点及现有管理基础,从精益角度给定其改善整体步骤:
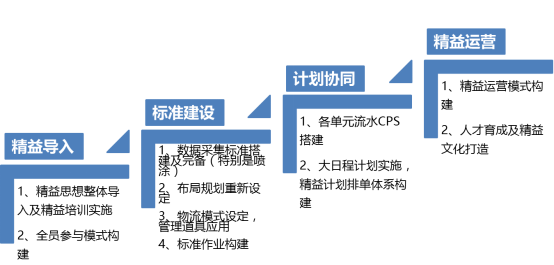
从精益思维导入开始,全员化精益模式推进,构建相应组织及机制,奠定精益管理基础;
3.2.2精益模块导入方式方法
3.2.2.1、某汽车行业MES系统软件基础数据采集补充、作业标准化构建
a. 针对喷涂车间涉及到的所有产品进行P/Q分析;
b. 针对小批量多品种环境下需求进行产品分族设定,建立产品工艺穿插表及产品设备穿插表;
c. 根据P/Q分析,对分类产品进行标准工时测定(秒表设定或PTS分析);该工时测定要求细分到每个工序每个动作,对不同形态的设备、距离、材料放置方式都会有严格要求;
注:选定产品为工艺相似、设备相似作为产品族进行确认,根据工时标准设定流水线形态,根据P/Q分析先可选定1-2组进行测算,当在试验无误时进行全面推广。此数据为喷涂车间排产基础,排产执行到什么程度决定于该数据的细化程度。
d. 根据现有作业标准进行动作分割,建立标准作业组合表,确认每道工序标准作业形态;
e. 建立产品标准作业状态表,明确节拍时间、作业顺序;
f. 各个工序标准作业票的设定;
注:标准作业票为每个产品订单下达后的具体操作模式,此标准作业是常规的作业标准的细分与组合,相对产品族有比较雷同的作业模式;
3.2.2.2、某汽车行业MES系统软件单元流水的构建及布局优化
a. 根据物流走向重新设定布局规划;
b. 在各项作业标准被固化之后针对喷涂车间进行内部单元流水作业的排定并形成N个单元流水,配合喷涂工序完成计划作业;
c. 对总装、包装车间进行单元流水改造,针对能够进行流水生产的产品族进行工时分解、消除、组合,重新形成相应标准作业票,并根据相应节拍进行产线布局;
3.2.2.3、某汽车行业MES系统软件物料供应方式及供应频次规则设定
a. 物料种类划分,尺寸大小确认;
b. 车间内部流水线内部物料转运方式设计(搬运台车设计、台车容量、供应方式、赋码方式、频次时间的考虑);
c. 段状流水外部物料转运方式设计(搬运台车设计、台车容量、供应方式、赋码方式、频次时间的考虑);
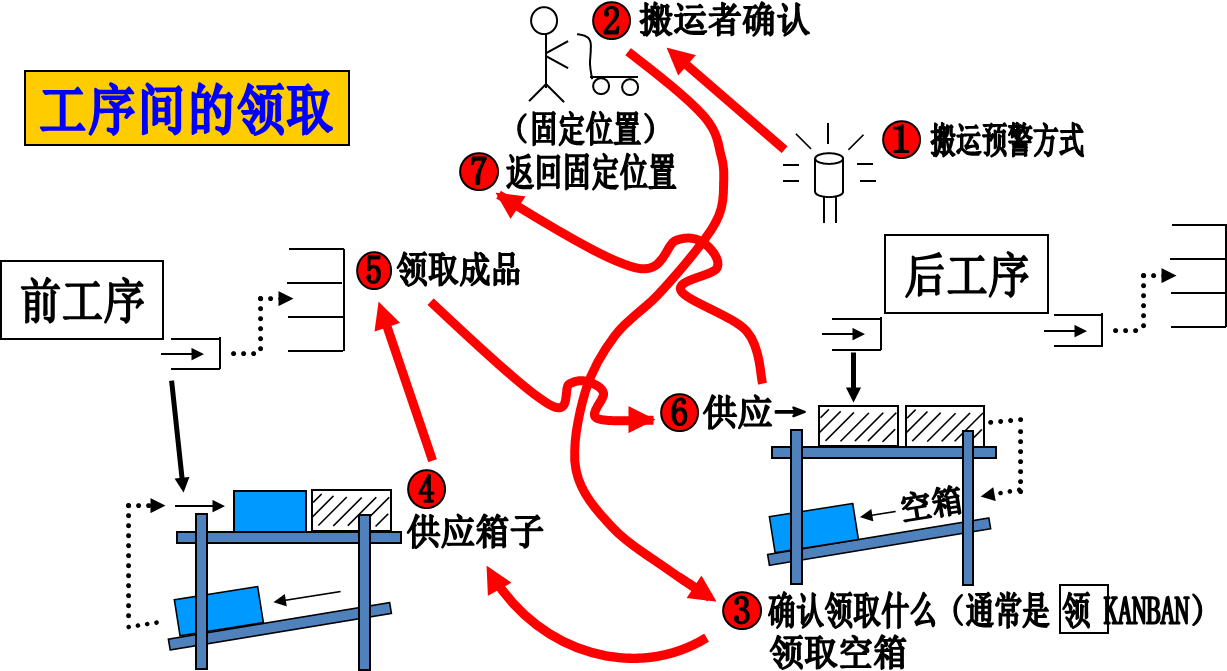
d. 物料供应频次及时间规则的确认(根据不同产品节拍时间不一致,物料供应频次及时间也需要重新设定)
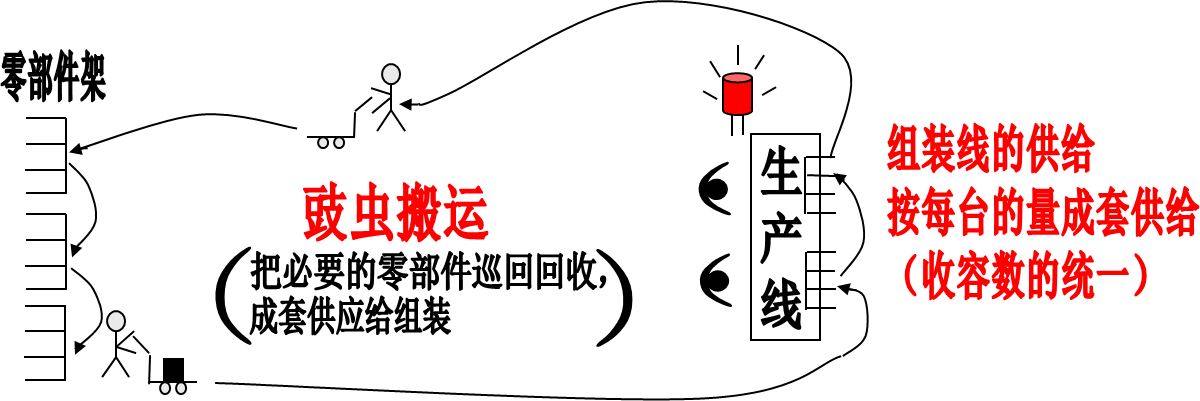
e. 逆向物流物料转运方式设计(品质问题台车设计、流转方式、赋码方式、识别方式)
f. 物料台车与物料一一绑定模式设计;
注:物料供应方式与产线节拍、台车设计方式等息息相关,并在供应时需要考虑台车与物料的一一对应及供应时的自动预警,在设计过程需要结合标准作业及订单的结合;
3.2.2.4、某汽车行业MES系统软件管理道具的应用
a. 产线管理看板的设计;
b. 线体物料架及放置模式的设计;
c. 工具台的设计;
d. 检验台的设计;
e. 不良品放置区域设计;
f. 教育台的设计;

3.2.2.5、某汽车行业MES系统软件生产段区域(喷涂车间)先进计划模式的设计
a. 设定喷涂车间区域流转模式,确认喷涂布局及优化;
b. 收集喷涂车间整体工序标准工时并确认喷涂实际生产前置时间;
c. 根据不同生产前置时间确认每款产品工艺流的走向;
d. 根据生产前置时间排定不同前置时间下各个零部件的喷涂生产计划,用以适应整个生产计划;
3.2.2.6、某汽车行业MES系统软件整体看板模式的设计
a. 外部原材料-注塑-喷涂-总装-包装及制版-组装包装推式看板设计(看板数量、看板运行规则);
b. 各个状态顺流转运方式物流看板设计(台车看板、线边仓看板等);
c. 各个状态逆流转运方式物流看板设计(台车看板、线边仓看板等);
d. 拉式看板设计。
3.2.2.7、某汽车行业 MES系统 软件整体拉动计划模式构建
a. 喷涂内部计划排布显性设计(工位设计及排布,单元流水设计,工时系统构建完备后可确认)
b. 整体排程方案设定(销售、采购、生产、技术协同模式的构建),失效模式分析及优先级分析并确认;
c. 整体订单优先级模式确认(如何优化订单及更改订单模式);
d. 优化排程:在满足订单交期的前提下,把所有生产任务(工序)分配到最合适的资源上生产,提高生产效率,资源利用率,减少生产成本。
各产品根据其产品结构、工艺路线生成产品工艺模型图,各工序之间关系,原材料与工序关系都一目了然。瓶颈资源重点优化排产,减少等待时间,换线时间,大幅提高生产效率。减少换线时间,排程时任务有多台资源可用时,自动分配到换产时间最少的资源上加工。最大限度安排工序之间并行生产。前工序完工一批,后工序即可安排进行生产,多工序看起来像并行生产一样,大幅缩短产品加工周期。合理安排加班、调休,对于某些资源最近生产任务量少的,严重不饱和,建议调休或调产线,把工作时间节省出来以备将来加班。对于某些资源最近生产任务量大的,超负荷而且导致订单延期交货的,可安排加班。工序的可开工时间,考虑前工序的计划完成时间,和原材料的到料时间,保证计划的可行性。订单出现延期时,可采取提高优先级、增加资源生产、工序并行生产、工序委外等措施。
公司整体布局及工序分布相对合理,整个物流走向按照工艺流程进行布置,由于厂房设计及工艺限制,将各个工序进行分车间管理,主要分为注塑、制版、喷漆、总装、包装及仓储几个车间,主要工艺流程如下(制版及分装未纳入):

在整个工艺流分布过程中,喷漆车间为工艺分割最多的车间,其工艺复杂程度较高,并分成了几个独立的小模块,该车间管控难度较大,由于工艺问题上下工序衔接经常出问题,这也使得喷漆车间成为公司生产运营过程中的盲区,无法量化的工艺设定导致产品在该区域生产过程无法进行监控,该车间建立流水模式及数据采集显现的需求相对迫切。
从工艺走向来看,整个物流过程充满了搬运及WIP堆放的浪费,几乎每个工序都需要进行搬运和堆放,从精益角度看,每个工序都存在浪费;
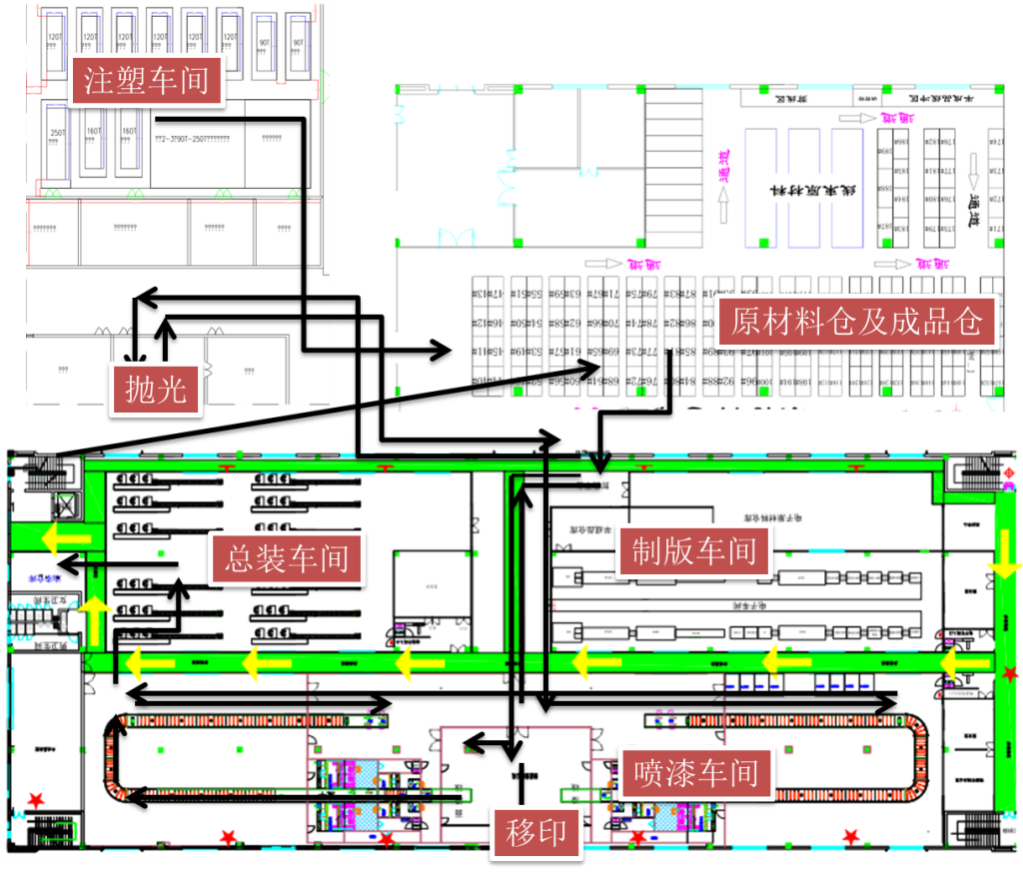
图3:公司产品实物流转图
在整个实物流转图中,由于布局的限制,使得注塑与其他车间的搬运距离相对较远,在喷漆车间内部出现的搬运情况较为严重,物料从原材料仓库到喷漆车间一直到从喷漆车间出去到总装,整个物流距离接近1800米(包含到抛光并返回),还不算工序内部兜转距离;车间内部搬运距离过长,使得喷漆整体无法把控。
内部物流主要依托流转小车及搬运车,但对搬运频次、搬运容量、搬运时间并未做相应标准,使得搬运过程随意性大。
3.1.2.4、内部计划协调性差,计划达成率不高
由于车间内部基础数据的缺失而无法进行工序工时估算、车间内部物流相对混乱而无法制定标准管理道具及辅助工具,使得公司在计划协调性上柔性不足,又由于销售预测及采购上的不确定因素过多,使得计划生产难度加大,销售被迫妥协生产,生产又由于订单及内部问题导致计划达成率低。
单从喷涂计划实施来看,整个计划模式在此车间运行几乎毫无规则,物流部针对喷涂下达的也仅仅只是周计划,无法落实具体的当日计划,更无法对喷涂进行产能管控,导致整个生产计划被喷涂计划全部打乱,依照模糊的计划进行生产的喷涂车间内部也没有进行相应的管控措施,包括物料供给方式也无法确定,使得喷涂车间变成整个生产部门的黑匣子,产品什么时候出来没有人能真正得知。
从计划实施上看,对于相对能够预估产能的车间部门,计划都制定了相应详细的周、日预估,而对于急需改进的喷涂车间却只有周计划,无法协同的生产模式注定每个区块的效率都无法达到最优值。

(图4、总体达成情况)
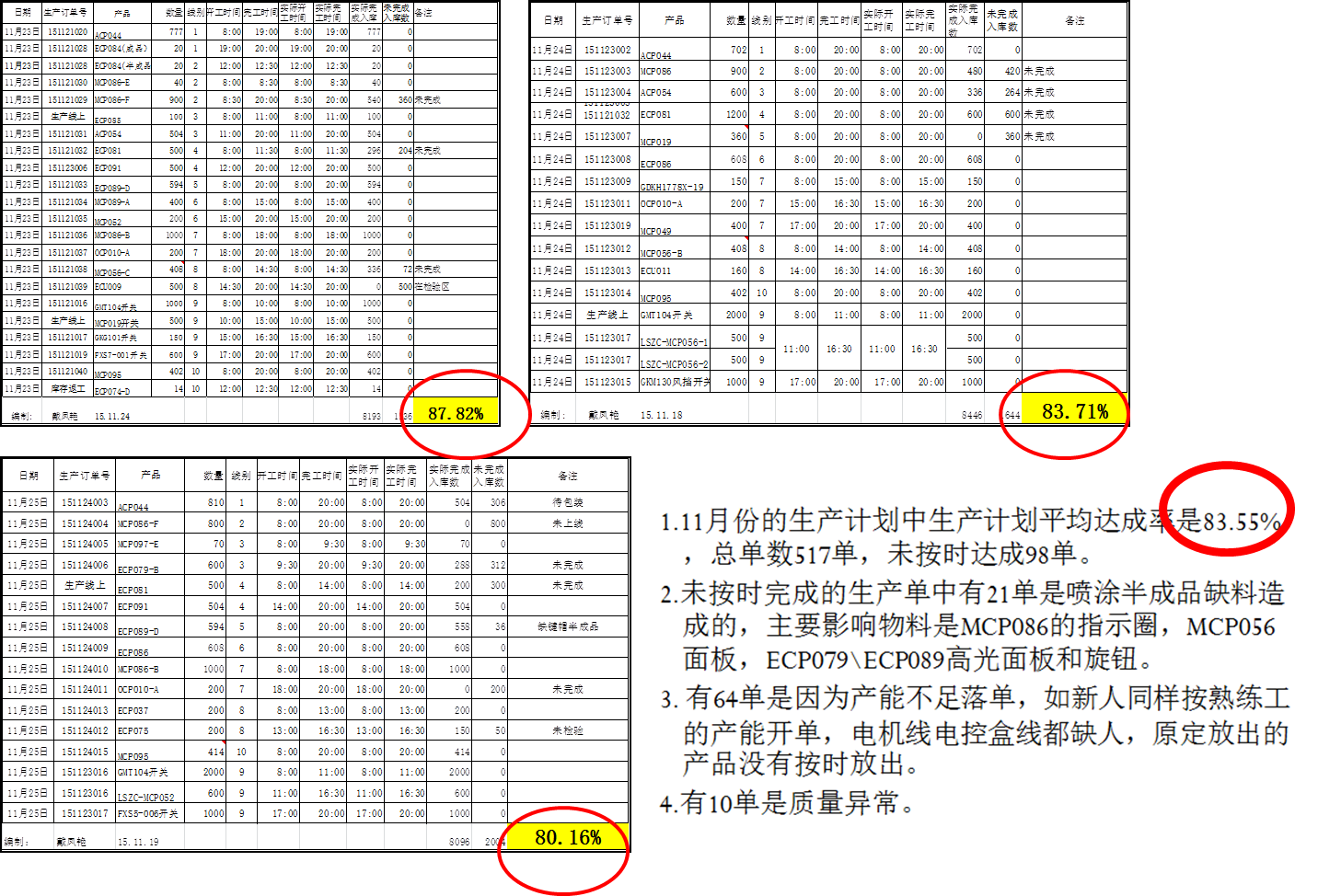
(图5、11月份计划达成率)
每个车间都有不同的生产计划,计划协同性及优先级无法整体体现,所以喷涂依据总装计划混合生产,销售插单将总装计划打乱,进而整个计划被打乱。
3.2 某汽车行业MES系统软件精益整体化解决措施
3.2.1 精益整体规划设计
某汽车行业MES系统软件精益整体理念构建框架:
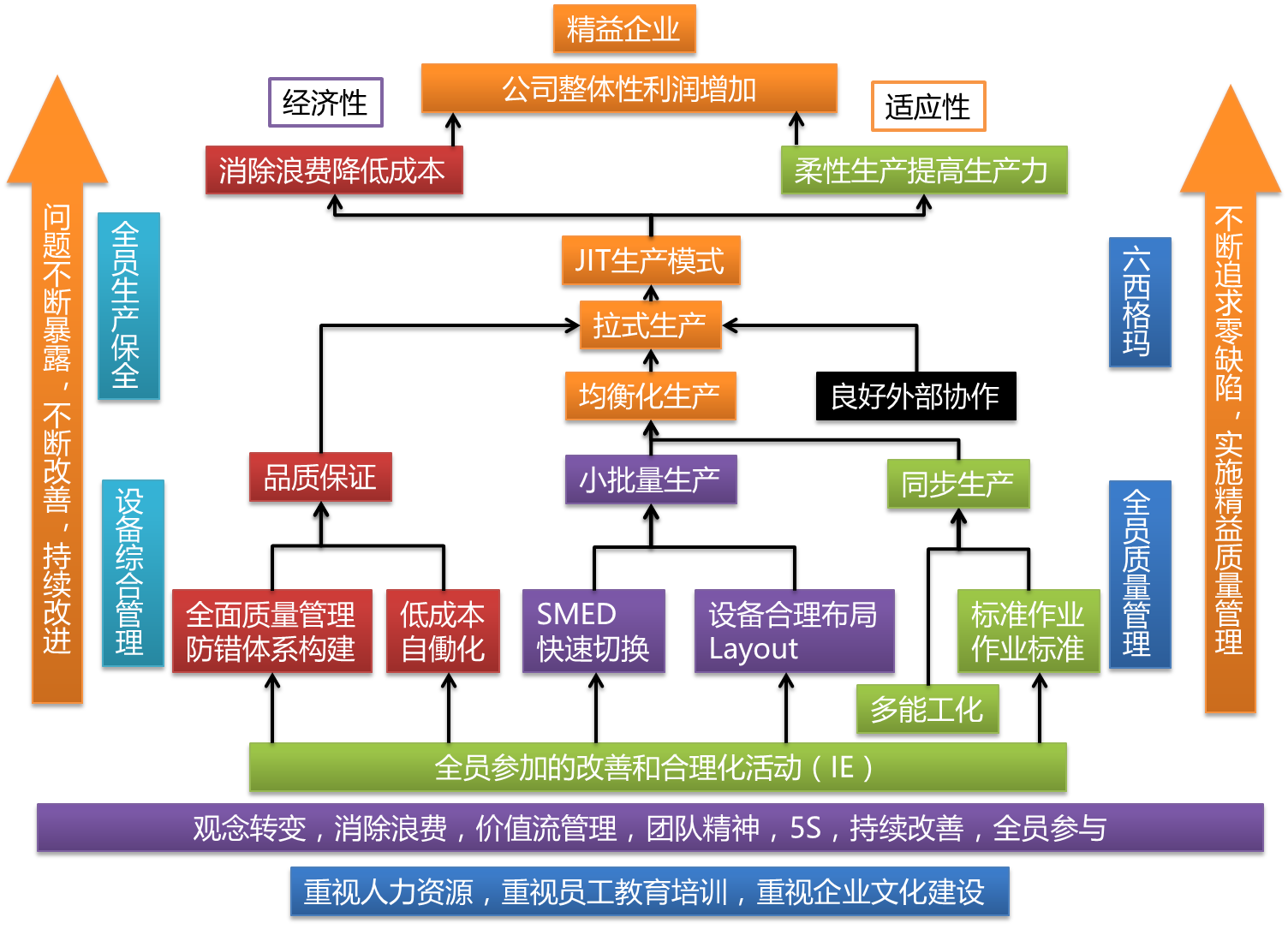
依据该公司管理特点及现有管理基础,从精益角度给定其改善整体步骤:
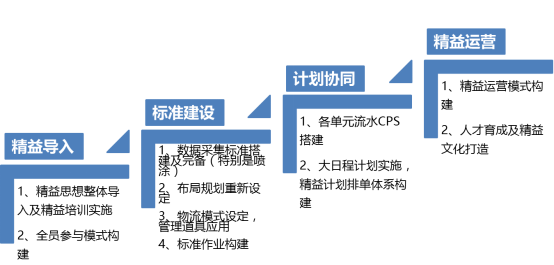
从精益思维导入开始,全员化精益模式推进,构建相应组织及机制,奠定精益管理基础;
3.2.2精益模块导入方式方法
3.2.2.1、某汽车行业MES系统软件基础数据采集补充、作业标准化构建
a. 针对喷涂车间涉及到的所有产品进行P/Q分析;
b. 针对小批量多品种环境下需求进行产品分族设定,建立产品工艺穿插表及产品设备穿插表;
c. 根据P/Q分析,对分类产品进行标准工时测定(秒表设定或PTS分析);该工时测定要求细分到每个工序每个动作,对不同形态的设备、距离、材料放置方式都会有严格要求;
注:选定产品为工艺相似、设备相似作为产品族进行确认,根据工时标准设定流水线形态,根据P/Q分析先可选定1-2组进行测算,当在试验无误时进行全面推广。此数据为喷涂车间排产基础,排产执行到什么程度决定于该数据的细化程度。
d. 根据现有作业标准进行动作分割,建立标准作业组合表,确认每道工序标准作业形态;
e. 建立产品标准作业状态表,明确节拍时间、作业顺序;
f. 各个工序标准作业票的设定;
注:标准作业票为每个产品订单下达后的具体操作模式,此标准作业是常规的作业标准的细分与组合,相对产品族有比较雷同的作业模式;
3.2.2.2、某汽车行业MES系统软件单元流水的构建及布局优化
a. 根据物流走向重新设定布局规划;
b. 在各项作业标准被固化之后针对喷涂车间进行内部单元流水作业的排定并形成N个单元流水,配合喷涂工序完成计划作业;
c. 对总装、包装车间进行单元流水改造,针对能够进行流水生产的产品族进行工时分解、消除、组合,重新形成相应标准作业票,并根据相应节拍进行产线布局;
3.2.2.3、某汽车行业MES系统软件物料供应方式及供应频次规则设定
a. 物料种类划分,尺寸大小确认;
b. 车间内部流水线内部物料转运方式设计(搬运台车设计、台车容量、供应方式、赋码方式、频次时间的考虑);
c. 段状流水外部物料转运方式设计(搬运台车设计、台车容量、供应方式、赋码方式、频次时间的考虑);
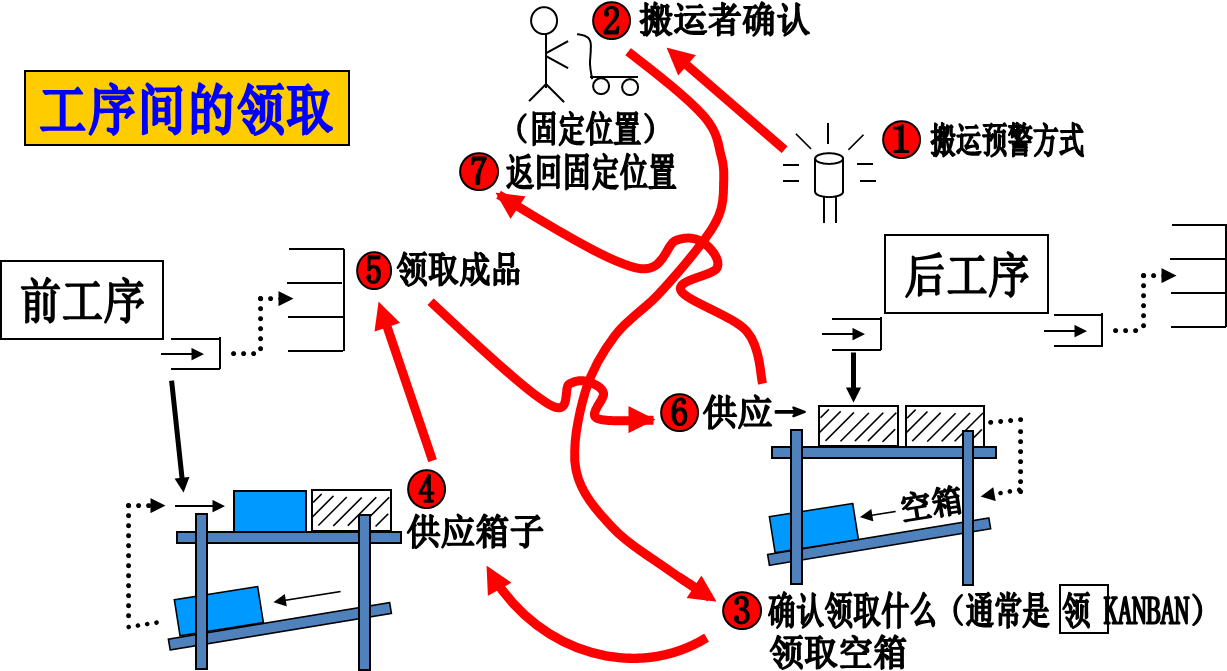
d. 物料供应频次及时间规则的确认(根据不同产品节拍时间不一致,物料供应频次及时间也需要重新设定)
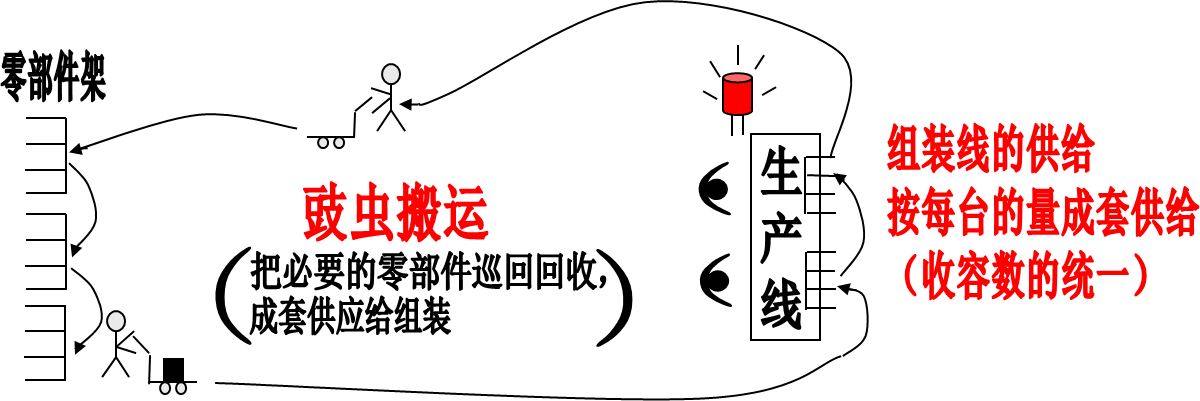
e. 逆向物流物料转运方式设计(品质问题台车设计、流转方式、赋码方式、识别方式)
f. 物料台车与物料一一绑定模式设计;
注:物料供应方式与产线节拍、台车设计方式等息息相关,并在供应时需要考虑台车与物料的一一对应及供应时的自动预警,在设计过程需要结合标准作业及订单的结合;
3.2.2.4、某汽车行业MES系统软件管理道具的应用
a. 产线管理看板的设计;
b. 线体物料架及放置模式的设计;
c. 工具台的设计;
d. 检验台的设计;
e. 不良品放置区域设计;
f. 教育台的设计;

3.2.2.5、某汽车行业MES系统软件生产段区域(喷涂车间)先进计划模式的设计
a. 设定喷涂车间区域流转模式,确认喷涂布局及优化;
b. 收集喷涂车间整体工序标准工时并确认喷涂实际生产前置时间;
c. 根据不同生产前置时间确认每款产品工艺流的走向;
d. 根据生产前置时间排定不同前置时间下各个零部件的喷涂生产计划,用以适应整个生产计划;
3.2.2.6、某汽车行业MES系统软件整体看板模式的设计
a. 外部原材料-注塑-喷涂-总装-包装及制版-组装包装推式看板设计(看板数量、看板运行规则);
b. 各个状态顺流转运方式物流看板设计(台车看板、线边仓看板等);
c. 各个状态逆流转运方式物流看板设计(台车看板、线边仓看板等);
d. 拉式看板设计。
3.2.2.7、某汽车行业 MES系统 软件整体拉动计划模式构建
a. 喷涂内部计划排布显性设计(工位设计及排布,单元流水设计,工时系统构建完备后可确认)
b. 整体排程方案设定(销售、采购、生产、技术协同模式的构建),失效模式分析及优先级分析并确认;
c. 整体订单优先级模式确认(如何优化订单及更改订单模式);
d. 优化排程:在满足订单交期的前提下,把所有生产任务(工序)分配到最合适的资源上生产,提高生产效率,资源利用率,减少生产成本。
各产品根据其产品结构、工艺路线生成产品工艺模型图,各工序之间关系,原材料与工序关系都一目了然。瓶颈资源重点优化排产,减少等待时间,换线时间,大幅提高生产效率。减少换线时间,排程时任务有多台资源可用时,自动分配到换产时间最少的资源上加工。最大限度安排工序之间并行生产。前工序完工一批,后工序即可安排进行生产,多工序看起来像并行生产一样,大幅缩短产品加工周期。合理安排加班、调休,对于某些资源最近生产任务量少的,严重不饱和,建议调休或调产线,把工作时间节省出来以备将来加班。对于某些资源最近生产任务量大的,超负荷而且导致订单延期交货的,可安排加班。工序的可开工时间,考虑前工序的计划完成时间,和原材料的到料时间,保证计划的可行性。订单出现延期时,可采取提高优先级、增加资源生产、工序并行生产、工序委外等措施。
作者:hzjuxadmin
推荐内容 Recommended
相关内容 Related
- MES系统,生产制造很给力01-09
- MES系统中生产运行系统的重要性01-08
- MES系统三大层结构01-07
- MES系统的五大功能、六大好处01-06
- MES系统与ERP系统的数据交互01-03